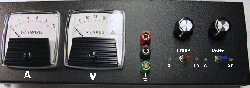
Bench Top Powersupply -- Part 2
"In this second part of the Bench Top Power Supply project we will
cover the construction, assembly, and wiring of the large coolrib and the
optional Automatic Fan Control circuit. When that is done the transformer T1,
115VAC components, large capacitor C3, and the bridge rectifier will be
installed and wired up. There are lots of pictures and photos to help you out.
Main thing to remember is to TAKE-IT-EASY, read the explanations and take your
time. This is definately a NO rush job."
by Tony van Roon,
VA3AVR
The Large Coolrib:
Building the large
coolrib was a lot of fun. I found an old coolrib in one of my parts boxes which
measured about 11" x 4-1/8" (28 x 10.5cm) which is perfect because it fitted the
back of the Hammond Instrument Case perfectly with room to spare for the AC-side
(see photo). The Hammond Instrument Case is not cheap, but is a ventilated,
low-profile, series 1426V type with dimensions of about 12x8x4 inches. Make sure
your transformer fits your instrument case!
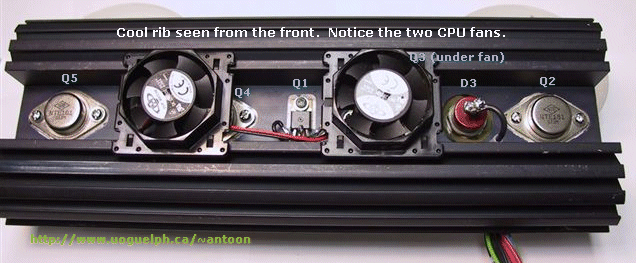
Looking at the photo above, it shows the large coolrib
with the two cpu fans. Since that picture was taken I have upgraded to three
ball-bearing cpu fans which have more blades and run quieter. They also are of a
different model and required a bit of tinkering to mount them on the coolrib
without drilling more holes. But that's the fun part of it, making things fit
and work. I didn't say building this power supply was easy, well, what I mean by
that is that some stuff needs to be modified in order to use it. I mounted the
fans in such a way so they blow the cool air over the semiconductiors and the
coolrib instead of sucking the hot air away from it.
Try to do a good job
on the coolrib, it'll pay later down the road. I mention this because we are not
all Tool-and-Die mechanics and for some of us this can be a real chore. But
don't worry, just take your time and you get it done. It took me almost a week
on and off.
Before starting to mount the transistors and power diode D3,
make sure all the holes are drilled. Take a large drill bit and remove the
burrs.
Including several extra holes to feed the wires through from D3, the
transistors and a spare just in case. Once everything is wired and bolted
together it is pretty hard to drill any hole anywhere. I'm not inclined to give
drill bit #'s and hole sizes at this time. Just make sure the holes are large
enough to snug-fit the plastic hole-insulators. Mount the TO-3 power 2N3772 (or
NTE181) transistors, Q2, Q3, Q4, and Q5. Use silicon heatsink compound on all
semiconductors mounted on the coolrib, between coolrib, mica-washer, and
transistor. Use insulators to screw down the transistors. Use the photo's and
drawings as a guide if you are not familiar with this method. That done, mount
the TO-220 transistor Q1 (2N6388 in my case). Again, make sure it is mounted
insulated.
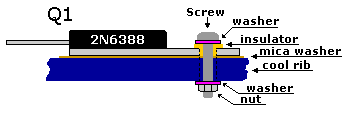
Power diode D3, needs some pre-work if you use the stud-mounted
model, like I did. The two mica washers and heat-shrink tubing
makes sure that this component also is insulated from the coolrib (see
pictures). Note again that D3 uses mica washers on each side of the coolrib and
a bit of heat shrink tubing in between, the size of the thickness of the
coolrib, to prevent the stud from touching the coolrib via the inside of the
mounting hole. You need to drill the hole a little bigger to account for the
extra thickness of the heat shrink tubing. Shrink the heat-shrink with a
hairdryer or something to make it a sturdy fit.
Try to make it a good fit as possible inside the mounting hole but
not tight. Meaning, after you drill the two holes for D3, one for the
stud-mount, the other to feed the wire through, check if the diode with the heat
shrink fits the hole. If not, don't use force and drill it a little larger or
use a small round file. Remove all the burrs from the holes with a large
oversized drill to prevent shorts. The nut of D3 faces towards the back. I left
the photo's pretty large so you can have a better look. For good heat transfer
from the semiconductors to the coolrib, use silicon heat-sink compound/paste of
some sort. They come in clear and white colors. Use it also on the power diode
d3.
When all semiconductors are mounted, and BEFORE
starting to wire the whole thing up, take your continuity tester or multimeter
and verify that the body of all transistors and the stud of D3 are insulated
from the coolrib and each other, meaning NO continuity on all of them.
One probe on the coolrib and with the other your check the semiconductors If all
is well, proceed, if not and you notice continuity somewhere it means that that
part is not insulated properly. Fix that first!
Click on the D3
photo's for a full-size view.
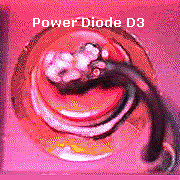
Making a good
and solid Printed Circuit Board will have its own awards.
The trimmer pots for 'voltage' and 'current' adjustments are logically grouped
together for neatness and ease of use. Use thick wire to connect the collectors
of Q2 to Q5 to the positive of C3. By full scale in the 10 amp setting there is
10 amps going through. Thick wire is mandatory or it will burn. Do the same for
the wire going from the minus of C3 to the common ground connection on the pcb
(see lay-out). From this point to the output studs, thick wire also. Make sure
large capacitor C3 is mounted isolated from the case or else, because of large
currents, weird things may happen inside the case. C5 and C6 must be of the
tantalum variety, nothing else!
When you mount the pcb in the case,
remove the copper around these screws so the pcb will be isolated from the case.
This method will prevent unwanted spurious ground loops.
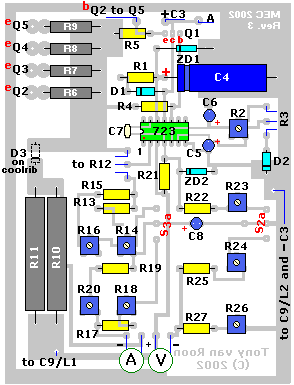
There was an error with the printed circuit board
(Rev.2). If you have this pcb version check below how to fix
it.
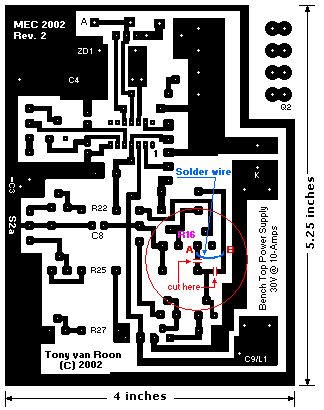
Wire-wound resistors R10 and R11 need to be mounted
'raised' from the pcb because they may get hot and placing them on ceramic
standoffs or something will prevent burning the pcb in that area. Diode D3 and
transistor Q1 are drawn on the layout but are actually mounted on the large
coolrib, so take note.
When you are ready to wire up the switches then it is
important to know that they are drawn in the 30-volts (S2a) and 10-amps (S3a)
positions. Dimensions of the PCB are: 4 x 5.25 inches or 295 x 385 pixels for
Paint Shop Pro. The pcb shown above is NOT to scale.
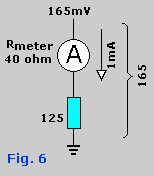
The Panel
Meters:
A big boy like this Jumbo power supply earned to have
a set of good panel meters. In the prototype a set of 1-milliamp full-scale
units were used. But I leave it to your own fantasy and creativity how to solve
the problem to enhance the overal cosmetic view of this power supply. As you can
see on circuit diagram (Fig. 5, Part 1), both meters have four switching
resistors. Two of them are mounted permanent in series with the measuring
system, the other two are paralleled by means of a switchable
section.
You should get panel meters with a very low own current use and
on top of that if possible types with 30 or better still 60 indicator stripes
(or markings) on it. A low current usage also means a low internal resistance
(Ri) which will benefit in the area of current measurement of that
particular panel meter. We assume that in the low 0 to 1-amp setting there are
only small voltages available over R10-R11 and if all goes to plan is the
maximum voltage around 165 millivolt and that is for low-ohm meters feasible.
So, try for a model with about 100 millivolt at full-scale. Which means that a
100 millivolt type only pulls 1 milli-amp at full scale. A 100µA type will have
a Ri of about a 1000 ohm. Check it yourself with Ohm's Law. For the
current panel meter try to get a type with 50 or 100 indicator stripes (or
markings). This is less critical for the 'Volt' unit. Basically you can use any
model as long as its own power is not higher than a couple milli-amps. The
internal resistance or Ri is less important since any type of internal
resistor will be removed anyways.
To calculate these resistors (R17 to
R20 for current, R24 to R27 for voltage), you have to determine
your meter's specifications. And here again, play with Ohm's Law. Point is that
in both cases, for current and voltage, we measure voltage every time.
For the measurement of current is 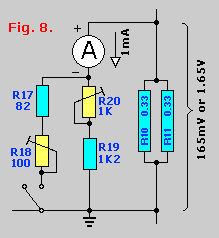
that 165 millivolt in the 1-amp position and 1.65 volt in
the 10 amp position. An example is given to make that very clear. Imaging we
have a unit which at full deflection pulls 1 milli ampere and has an internal
resistance of 40 ohms. If we want this unit to measure 165 millivolts then we
have to calculate the values as shown in the Fig. 6.
example. The 165 mV is the voltage, so the current has to be 1
milli-Ampere, using ohm's law that gives us a total resistance of 165 ohms. This
is the total resistance of everything. To get the value of the shunt resistor
just deduct the internal resistance. So, the shunt resistor has to be exactly:
165 - 40 = 125 ohms. To comfortably be able to adjust the meter's deflection we
devide this up in regular resistor of 68 ohm and a trimmer pot of 100 ohms. The
desired value of 125 ohms lays somewhere in between. But we are not done with
that. We still have to take the 1 - 10 Amp setting in consideration because
there are already a couple shunt resistors in series with the meter and those
are the components for the 10 amp scale. Looking at the example in Fig. 7, we have to measure there 1.65 volt and that means a
resistance value of 1650 minus 40 is 1610 ohms. This weird resistance value can
be obtained with a regular 1.2K resistor and a trimmer potentiometer of
1K.
The required value of 125 ohm can be acquired by adding another resistor
parallel with the funny 1610 ohm one. Doing the math (ohm's law), it turns out
the value of this parallel resistor is about 135.5 ohms and that is easily
obtainable with a 68 ohm resistor plus a 100 ohm Bourns trimmer potentiometer.
And if you're a perfectionist you can even choose a 82 ohm and a 100 ohm trimmer
potentiometer. In the end you will be getting something as shown in Fig. 8. If you have different types or values of panel meters,
the math is exactly the same. The trimmer pots with do the rest.
The
indication for the Volt-meter is similar. Note that we have taken a 500µA meter
as an example! I mention again, you have to find out the
characteristics for the meter YOU are using. (No, I will not do
the math or other calculations, please do it yourself I don't have the time). It
is not all that difficult. Simply assume we're gonna measure in the 6 and 30
volt ranges which happens to occur with a lot easier resistor values. Let's say
we have a panel meter with an 'internal resistance' of 3000 ohms and that at
full-scale it uses about 500µA, then the shunt resistors are looking like this:
for 30 volt the circuit needs a total resistance of 60K, so we need a 57K as
shunt which is put together of a regular 47K resistor plus a 20K trimmer
potentiometer. For the 6 volt scale we need a total shunt of about 9K which is
put together by putting a 10.7K resistor parallel with a 57K resistor. Again a
strange value but 8.2K plus a 5K trimmer potentiometer will make it work. In
Fig. 9 I used, where ever I could, metalfilm resistors
instead of the regular carbon type. They are more temperature stable. But carbon
types will work fine.
Question about filter chokes, L1 and L2? Why are
they there and what exactly do they do? They are there to eliminate the
switching noise that could otherwise possibly interfere with other equipment
(like a frequency counter). If you can't obtain the regular ferrite-bead type,
you can use the toroid type (from an old pc power supply) that filters the +5V.
Works good.
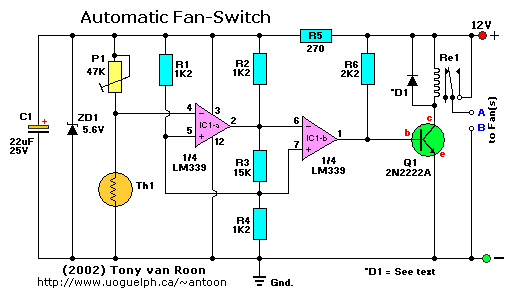
Shown
above is the circuit diagram for the automatic temperature control switcher. The
thermistor, a 1.7K at 70°F model available from Radio Shack (not sure), will
keep tab on the coolrib's temperature (adjustable with a 10-turn trimmer
potentiometer P1) and activate the cpu fans (or one larger fan) to keep things
cool. This circuit is not part of the Power Supply PCB at this time, but (given
time) I will change that early in the new year. I played with several different
value thermisters; 1.7K, 5K, 10K. They all worked fine after playing with the
resistor network a bit.
The D1 diode can be a signal diode like the 1N914 or
1N4148 for micro relays, use a 1N4001 or higher for relays above 100mA. D1 acts
like a spark arrestor/filter when the coil is de-energized.
Just in case,
here is another
circuit and this one Heat Sensor
using the more common 741 op-amp. Good circuits, working fine and a bit cheaper.
All parts are available from Radio Shack and Tandy. I found the 741-circuit
easier to adjust and there are no capacitors or zener-diode. But, make your own
choice. The "Heat Sensor" circuit works great and uses a minimum of easily
obtainable parts.
If you have any questions, I'll gladly answer them
via "Tony's Message Forum". I regret not answering personal
emails!
Back to Circuits Page or
Continue to Part
3
Copyright © 2002, Tony van
Roon (VA3AVR)
Last Updated: June 27,
2005